Отраслевые учёные быстро откликаются на актуальные проблемы железнодорожного транспорта, предлагая для их решения эффективные научные разработки.
Представленные исследования выполнены по инициативе специалистов МИИТа и ВНИИЖТа и не имеют аналогов в отечественной и мировой практике. Безусловно, до постановки новой продукции на производство необходимо проведение всесторонних исследований и испытаний. Однако уже имеющиеся результаты апробации новаций свидетельствуют о технологическом и техническом потенциале и высоком уровне их проработки для внедрения на сети ОАО «РЖД» и предприятиях отрасли, выпускающих продукцию для нужд компании. Предлагаемые разработки имеют высокую экономическую эффективность, позволят улучшить эксплуатационное содержание подвижного состава и инфраструктуры железных дорог, а также повысить безопасность движения.
Литые детали вагонов
Актуальность улучшения эксплуатационного содержания литых деталей вагонов, и в первую очередь их боковых рам, требует быстрых и эффективных решений как для обеспечения безопасности движения, так и по экономической составляющей. Например, при производстве термоупрочнённых железнодорожных рельсов их цена почти на порядок меньше, чем боковых рам тележек, но при этом есть большое количество вопросов к безопасности эксплуатационного содержания боковых рам.
В этой проблеме аккумулированы вопросы эффективности управления подвижным составом и его производства.
Традиционно вопрос повышения надёжности и долговечности тяжелонагруженных деталей подвижного состава решается за счёт увеличения толщины наиболее нагруженных их частей и деталей и применения стали с повышенным легированием. Оба способа приводят к дополнительным экономическим затратам и усложняют ремонтопригодность деталей.
Таким образом, локальную проблему по выходу из строя боковых рам вагонов следует решать в комплексе. Необходимо, чтобы качественно работали упругие элементы тележки и узел гашения колебаний.
По заданию Департамента технической политики ОАО «РДЖ» МИИТ на собственные средства провёл экспериментальную работу по объёмно-поверхностной закалке фрагментов боковых рам из стали 20ГЛ на организованном опытно-промышленном участке термического отделения на ОАО «Люблинский ЛМЗ».
К сожалению, в настоящий момент завершается ликвидация Люблинского ЛМЗ. На этом предприятии может быть закрыт опытно-промышленный участок, где разрабатывается технология упрочения боковых рам. Это обстоятельство может отдалить выдачу на эксплуатационные испытания боковой рамы с новым уровнем свойств на неопределённый срок.
Ранее проведённый комплекс исследований и полигонных испытаний объёмно-поверхностной закалки показал, что на таких литых деталях вагоностроения, как корпус автосцепки, буферные стержни пассажирских вагонов, замки автосцепок, хомуты автосцепок, фрикционные клинья и планки, корпуса поглощающих аппаратов, корпуса букс, достигается 3–5-кратное увеличение срока службы в эксплуатации. При этом затраты на переход к объёмно-поверхностной закалке по сравнению с серийным производством увеличиваются всего на 5–8%, что обеспечивает окупаемость новой технологии за 5–7 месяцев.
Однако её развитие сдерживает отсутствие заинтересованности производителей вагонов в её внедрении, а также действующие технические требования при производстве запасных частей и новых деталей вагоностроения.
Метизы
Объём выпуска метизов для железнодорожного транспорта самый большой по сравнению с другими потребляющими его отраслями промышленности. Поэтому долговечности их использования придаётся огромное значение. Исследовательский центр «Промышленные технологии и ресурсосбережение на транспорте» МИИТа самостоятельно исследует, разрабатывает и внедряет эффективные способы их упрочнения при минимуме затрат. В настоящее время закончены поисковые работы по объёмно-поверхностной закалке метизов.
В результате предел прочности на растяжение шурупов путевых двукратно увеличился по сравнению со стандартным производством.
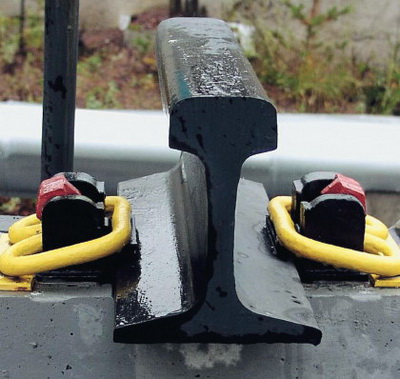
Кроме того, при использовании этого метода не требуется замена стали Ст3 на Ст20, что и позволяет существенно сэкономить средства.
Не менее важно, что термообработка стыковых болтов М27 из стали 35 по новой технологии позволяет получить на них класс прочности 10.9 против 8.8, как это происходит при стандартной процедуре. Для нормального эксплуатационного содержания пути с современным уровнем нагруженности требуется применение стыковых болтов именно этого класса.
В промышленности получить такой высокий класс прочности можно только за счёт использования легированной стали 40Х (1% Cr) и закалки в масле. Но при этом возрастает стоимость деталей, а также возникает неблагоприятная экологическая обстановка не только в термических цехах, но и в целом по производству.
Это актуально и при производстве шпилек мостовых. Они в значительном объёме выходят из строя из-за низкой усталостной прочности стали 40Х. Решить проблему позволит новая технология по замене легированной стали и закалки в масле на рядовую углеродистую сталь 35 с закалкой технической водой.
Но для широкомасштабного внедрения метода на промышленных предприятиях необходимы данные от профильных подразделений ОАО «РЖД» по анализу повреждаемости этих деталей в эксплуатации.
Упругие клеммы верхнего строения пути
Упругие клеммы отечественных скреплений типа АРС и ЖБР являются одним из наиболее важных элементов, отвечающих за их работоспособность. Для обеспечения надёжной эксплуатации (релаксационная стойкость и циклическая долговечность) специалисты университета разработали новую технологию их производства из стали пониженной прокаливаемости 50ПП и упрочнение методом объёмно-поверхностной закалки.
На одном из российских предприятий изготовлены опытные партии клемм и проведены стендовые испытания. Они показали, что за счёт их высокопрочного состояния получен уровень релаксационной стойкости, не достижимый для клемм серийного производства. Кроме того, обеспечивается более высокая циклическая долговечность.
Проведение расширенных полигонных испытаний и организация производства по выпуску клемм такого качества невозможны без заинтересованности Департамента пути и сооружений ОАО «РЖД» во внедрении новой технологии. На эти цели от металлургов получена промышленная плавка (20 тонн) новой стали.
Клееболтовой стык
Завершена разработка новой технологии, обеспечивающая улучшение эксплуатационного содержания клееболтовых стыков (КБС) и снижение их стоимости на 25–30% по сравнению с КБС, которые в настоящее время поставляются на магистральный транспорт.
Её главной особенностью является применение препрега на клеевой основе с конфигурацией, повторяющей профиль рельса. Этот метод устраняет влияние человеческого фактора, как это происходит при стандартном изготовлении стыка, а также не требует использования металлической обечайки. Металлические накладки изготавливаются из обычной углеродистой стали с конфигурацией, не требующей дополнительной механической обработки. На стык разработаны и утверждены технические условия. Стендовые испытания показали соответствие КБС новой конструкции требованиям норм безопасности на указанные изделия. Нормативная документация и результаты испытаний переданы в Центральную дирекцию инфраструктуры и в Департамент пути и сооружений ОАО «РЖД».
Экономичность изготовления и простота сборки стыка позволяют рекомендовать эту технологию для внедрения как в стационарных условиях, так и в полевых.
Намагниченность
Значительное количество сбоев в системах автоматической локомотивной сигнализации продиктовало необходимость провести исследовательские работы по созданию оборудования по размагничиванию и для контроля намагниченности, что позволило бы устранить причины, напрямую влияющие на безопасность движения.
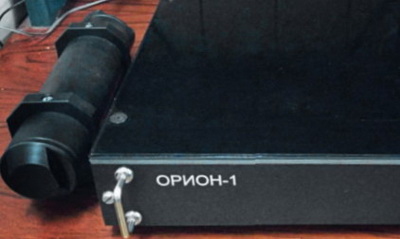
При активной поддержке Центральной дирекции инфраструктуры компании специалистами МИИТа создано измерительное оборудование по замеру намагниченности (метод магнитной локации) и размагничивающей системы, которое пригодно для работы в пути и стационаре. Оборудование смонтировано на вагоне-лаборатории «МИКАР» московского отделения дирекции. Проводить мониторинг на сети дорог по измерению магнитного поля рельсов и элементов стрелочных переводов, находящихся в эксплуатации, позволяет подвижный комплекс «Орион-1».
Последние измерения проводились на полигоне Белорусский вокзал – Савёлово.
Дополнительно был создан прибор «Орион» для замера намагниченности в условиях металлургических комбинатов, стрелочных заводов, рельсосварочных предприятий, контролирующих индукцию магнитного поля рельсов до их укладки в путь. Оборудование «Орион-1» для «МИКАР» и «Орион» для стационара подготовлено к выполнению требований ГОСТ по постановке продукции на производство и комплексной оценке их работоспособности комиссией ОАО «РЖД».
Чтобы определить степень намагниченности полигона железных дорог, были организованы опытные поездки «МИКАР» (мониторинг по движению «Сапсана» на Нижний Новгород и на МЖД). Они показали, что наибольшее превышение фиксируется в местах укладки изолирующих стыков из стеклопластика, который не пропускает магнитный поток. Поэтому предприятиям, выпускающим изолирующие накладки, следует использовать при их производстве шунтирующие элементы.
Для внедрения перечисленных выше разработок в производство и их практического применения необходима активная помощь ОАО «РЖД». И, если новые технические решения и технологии вызовут у специалистов холдинга интерес, МГУПС готов к сотрудничеству и совместной реализации этих проектов.
СПРАВКА
Анализ существующих способов упрочнения деталей показывает, что метод объёмно-поверхностной закалки, разработанный в нашей стране для средне- и высоколегированных сталей, может быть эффективно применён для низкоуглеродистых (0,17–0,25%) сталей.
СПРАВКА
В результате объёмно-поверхностной закалки физико-механические свойства стали увеличились. Предел прочности и износостойкость – на 40%, величина остаточных сжимающих напряжений достигает 200 МПа (после нормализации – растягивающие напряжения 50 МПа), поверхностная твёрдость – 30–45 HRC, усталостная прочность увеличивается на 10%, что позволяет улучшить эксплуатационное содержание боковой рамы. Причём достижение такого уровня свойств обеспечивается без значительного увеличения затрат.