Полвека назад производственная система японского концерна Тойота (TPS) перевернула представление бизнеса о производстве, отношении к сотрудникам, партнёрам. Меняется экономическая конъюнктура, но принцип максимально быстрого, дешёвого и эффективного удовлетворения потребностей заказчика не устаревает. Сегодня эту философию разделяют все крупные мировые компании: от банков до предприятий атомной промышленности.
В условиях жёсткой конкуренции при ограниченности собственных ресурсов создание производственной системы иногда становится единственной возможностью выживания бизнеса.
Точка отсчёта – кризис
Неблагоприятные внешние факторы – это всегда катализатор внутренних изменений. Кризис вынуждает оптимизировать затраты, снижать себестоимость. Коллапс мирового финансового рынка в 2008/2009 году заставил нас переоценить издержки, понять, на каких этапах и что к ним приводит. До тех пор «РУСАЛ» пробовал создать TPS только на отдельных заводах, но именно в этот момент началась серьёзная системная работа.
Конечно, это не значит, что формировать культуру улучшений можно и нужно только в кризисный период. Посыл должен быть другой – потребность изменений в компании. Когда руководство понимает, что притока свежих идей нет, даже стабильному и прибыльному предприятию понадобится культура улучшений. При этом без инициативы и постоянной поддержки первых лиц не стоит ждать долгосрочного эффекта. Можно за две недели оптимизировать работу на любом производственном участке и даже получить результат, но пока персонал не проникнется философией улучшений, это будет только разовая акция.
Не случайно все эти годы «Тойота» непрерывно совершенствует свою систему, выявляет новые потери, находит возможности улучшений, создаёт условия для развития своих сотрудников. Японцы не ждут аварийной ситуации, чтобы решить проблему. Они заранее выявляют «узкие» места и по максимуму вовлекают операционный персонал в обслуживание оборудования.
По их примеру наши ремонтные службы совместно с эксплуатацией сейчас осваивают автономное обслуживание, тогда как раньше приступали к ремонту только при сбоях. Так была построена ещё советская система. «РУСАЛ» для предупреждения аварий сделал ещё один шаг. На всех заводах к этому моменту созданы комнаты производственного анализа, где в режиме реального времени можно отслеживать показатели по всему потоку, начиная от поставки сырья и заканчивая передачей готовой продукции потребителю. Это открытое помещение, и доступ туда имеет любой рабочий.
Производственная система как раз и хороша тем, что решения сложных вопросов обычно достаточно просты и предложить их может каждый. Когда-то на ИркАЗе, в литейном отделении потери времени при переналадке ленты прокатного станка составляли 1 час 50 минут. Всего лишь перераспределив и запараллелив процессы между операторами и вынеся многие действия во внешнюю переналадку, когда оборудование ещё работает, мы сократили время выполнения этой работы до 10 минут. Компания не потратила ни копейки на модернизацию, не нанимала новых, более профессиональных специалистов. Операцию по-прежнему выполняют наши обычные литейщики и ремонтники, только с большим эффектом и меньшими издержками.
С самого начала мы понимали, что использование каких-то готовых решений или развитие одной команды в роли проводника улучшений – путь в никуда. Эти меры годятся для получения сиюминутного результата, но в расчёте на перспективу малоэффективны. Другое дело – создание системы для изменения модели поведения сотрудников. Примером для нас стала классическая TPS и производственная система ГАЗа – первопроходца среди российских компаний. Мы даже приглашали конструкторов с ГАЗа для совместной работы. На производстве им показывали, какие операции нужно механизировать, а они предлагали нам какие-то конструкторские решения.
Но даже имея перед глазами успешный опыт, пытаться распространить его сразу на все заводы и предприятия – всё равно, что объять необъятное. Невозможно быстро поменять представления тысяч людей. Каковы бы ни были предлагаемые изменения, психологи давно доказали, что за и против категорично выскажутся 10% работников, а 80% – будут колебаться. Вот за умы этих 80% и разворачивается основная борьба.
Как же распространить новый, более эффективный способ организации производства, не навязывая персоналу «чуждую» ему философию? Ответ прост: мотивировать, поощрять, обучать работников действовать в новой системе координат на небольшом, но ключевом участке. Через какое-то время эти пилотные участки, как локомотивы, будут разгонять производственную систему в компании.
Фокус на персонале
То, что мотивирует одного сотрудника, не всегда достаточный стимул для другого. Прежде чем массово вовлекать персонал в новую для них производственную систему, нужно чётко понимать, что и от кого мы хотим, на кого будем опираться: руководителей разного уровня, линейный персонал, рабочих. Взять, к примеру, топ-менеджмент. Раз в квартал все члены правления «РУСАЛа» во главе с генеральным директором в составе так называемых управляющих комитетов выезжают на один из заводов и на примере конкретных промышленных площадок оценивают динамику развития TPS. Для руководства это возможность получить информацию из первых рук и ознакомиться с практическим опытом, для завода – шанс рассказать о достижениях и потребностях, для работника – серьёзная мотивация. Получается, мы одновременно вовлекаем топ-менеджмент в процесс изменений и повышаем лояльность персонала.
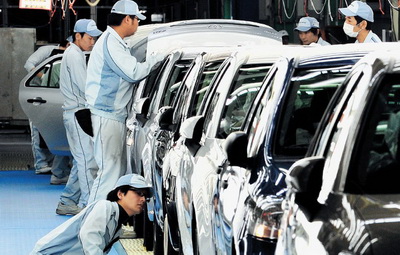
Но главная наша задача – воспитание работников в культуре улучшений. Вкладываться в массовую переподготовку чересчур затратно и более того – бессмысленно. Поэтому у нас каждый год составляется список кандидатов на обучение из числа бригадиров и мастеров. Программа 2015 года, к примеру, рассчитана на 250 человек. С каждого завода участвуют примерно по 10–20 работников. Отбор идёт в несколько этапов.
На первом этапе перед кандидатами ставится задача, выводящая их за рамки повседневной деятельности. Это может быть увеличение производительности труда бригады, повышение эксплуатационной готовности, надёжности агрегата, в общем, то, что они могут сделать своими силами или с привлечением помощи, но на своём рабочем месте. На решение задачи отводится три-четыре месяца. Человек за это время либо проявляет себя, либо нет. Если нет – никаких репрессивных мер к нему не применяется. Наша задача не наказать, а выявить сотрудников с наибольшим потенциалом.
Как правило, из 250 кандидатов дальше проходит около сотни. Им поручается серьёзный проект по производственной системе, а параллельно компания обучает их основным подходам и принципам TPS, в том числе на эталонных участках. Работник пробует себя на других заводах и даже в других профессиях. Коммерсант на время становится мастером в электролизе, а мастер в электролизе – специалистом в службе персонала. В классической TPS «Тойоты» так на разных позициях пробуют каждого, кто туда трудоустраивается. Считается, что работнику нужно сменить три-четыре профессии, прежде чем найти подходящую.
Сито отбора определяет лучших из лучших. Они уже носители новой культуры улучшений. Их зачисляют в кадровый резерв, организуют зарубежные стажировки и обучение по программам MBA. Это будущее компании, и даже в кризисных условиях мы не прекращаем отбирать и обучать персонал.
Однако практика показывает, что предлагать интересные, эффективные улучшения способны и рядовые работники без специальной подготовки. Это обычно что-то простое и в то же время действенное. Естественно, мы их инициативы поддерживаем и, если есть необходимость, помогаем в реализации. Интерес сотрудников поддерживает дух соревнования.
Конкуренция – двигатель новаций
С 2010 года все заводы «РУСАЛа» проводят конкурс на лучшее улучшение – «кайзен года». Соревнование идёт в трёх номинациях: безопасность, качество и экономичность. Какое улучшение – затратное или нет, с большим или меньшим эффектом – предлагает работник, значения не имеет. В принципе, кайзен может вообще не принести экономического эффекта. Если речь идёт о безопасности условий труда, компания готова даже профинансировать проект. Единственное условие для участников – все улучшения к моменту конкурса уже должны быть внедрены на заводе. Для этого в «РУСАЛе» поддерживается система подачи кайзенов. В классической TPS в «Тойоте» работникам за них начисляются баллы, действует своего рода накопительная системы. Но мы пошли по другому пути. По примеру европейских компаний, в частности Bosch, новатору за небольшое улучшение выплачивается символическая сумма в размере 100–150 руб. в зависимости от завода. Это может быть поощрение за изобретение нового инструмента, изменение в подходах и стандартах выполнения операций. Есть и более креативные улучшения.
Пример такого народного творчества – проект – победитель конкурса улучшений прошлого года на КрАЗе. История вышла практически анекдотичная. Группа работников – любителей рыбной ловли выпустили выловленных небольших рыб в водоём, используемый как отстойник воды для литейных агрегатов, откуда вода поступает в производство. Рыбы очистили её, и стабильность вместе с качеством литья выросли. Вот так небольшой кайзен, который вообще ничего не стоил, принёс эффект.
Конкурс на лучший кайзен сразу приносит реальную экономическую выгоду компании. Только в прошлом году реализация проектов работников сэкономила нам $74 млн. Чем больше людей проникается философией улучшений, тем больше кайзенов они предлагают, чем больше кайзенов – тем больше желающих предложить свои идеи.
Для обострения конкуренции «РУСАЛ» проводит общекорпоративный конкурс улучшений. Победителей лично поздравляет генеральный директор, им даются небольшие премии и подарки. Получить награду и почётно, и полезно для карьерного роста. Конечно, сравнить конкурсантов с разных заводов достаточно непросто – культура улучшений везде разная. На Красноярском алюминиевом заводе производственная система внедряется с 2007 года, на заводе в Ирландии – с 2000 года. Логично, что и предложения улучшений там более серьёзного уровня. На многих предприятиях система только запускается, и это вполне нормально. Добиться быстрых изменений везде невозможно. Наша цель постепенное, но массовое распространение философии среди всех сотрудников.
Если символическое поощрение направлено на рабочих, мастеров, бригадиров, то есть низший управленческий состав и исполнителей, то для мотивации среднего звена у нас действует проектная система. Серьёзный эффект достигается, как правило, на границах взаимодействия разных подразделений. Здесь нужна командная работа, а в российских компаниях она традиционно слабо развита. На своём рабочем месте специалисты могут улучшить практически всё, но стоит начать работу с коллегами из других отделов, как сразу возникают проблемы. В этом, кстати, наша система очень похожа на японскую. Мы активно пытаемся устранить барьеры и выстроить, как говорят японцы, «команды без стен». Когда возникает некая бизнес-цель, требующая участия нескольких подразделений, «РУСАЛ» создаёт максимально благоприятные условия для инициаторов проекта. Вариантов много: быстрые инвестиции, возможности для обучения, посещение родственного завода или налаживание контактов коммуникации с потребителями и поставщиками.
Практика показывает, что оптимизация производственных процессов постоянно требует приложения усилий сотрудников разных отделов. Только слаженная командная работа логистов, железнодорожников, глинозёмщиков и алюминщиков позволила нам нивелировать затраты при доставке глинозёма. До недавнего времени его в вагонах доставляли на центральный склад алюминиевого завода, а оттуда – системой внутренних трасс до электролизёра. Чем дольше глинозём шёл по трубопроводу, тем больше истирался, мельчал и терял свои качества. Прибавить к этому потери при загрузке и разгрузке, пыление – и получалось около 600 кг необязательных расходов. Для таких случаев и нужна производственная система.
Решение проблемы оказалось простым – использовать биг-бэги. Теперь глинозём загружается в мешки, доставляется на алюминиевый завод и подвозится в обход системы подачи трубопроводов сразу к электролизёру в той последовательности, в которой идёт потребление. Потери снизились до килограмма, а производительность электролизёра выросла. Что мешало сделать это раньше? По сути, ничего, но никто не мог соединить идеи и реализовать процесс без глобальных перестроек.
Поощрение для инициаторов подобных проектов, конечно, более серьёзное. Новаторам выплачивается до 10% официально подтверждённого экономического эффекта. А возможностей получить такую прибавку для активного грамотного специалиста немало. Некоторые производственные процессы, требующие оптимизации, буквально на виду.
Долгое время, к примеру, под нужды заводов закупалась специализированная автомобильная техника, хотя в советский период она также изготавливалась у нас. К этой традиции мы сегодня постепенно возвращаемся и начинаем самостоятельно проектировать и выпускать технику, исходя из потребностей заводов.
В целом же кайзен-деятельность компании сегодня концентрируется на повышении надёжности оборудования – нашей основной единицы, приносящей ценность. Наша задача ликвидировать ремонтные простои и увеличить срок службы.
Но заводы не живут в какой-то замкнутой, ограниченной среде. Они контактируют с перевозчиками, поставщиками, покупателями, внешними структурами. Перемены внутри предприятия без попытки найти контакт и подвигнуть к изменениям партнёров бесперспективны. Можно подняться до определённого уровня, но дальше будет тупик.
Конечно, мы контактировали с теми же поставщиками и раньше, но недостаточно системно. И в прошлом году классическая производственная система «РУСАЛа» трансформировалась в бизнес-систему, сохранившую ядро культуры и основные принципы TPS, но нацеленную не только на изменение самой компании, но и на оптимизацию работы партнёров.
Международный подход
«РУСАЛ» не только производственная, но и логистическая компания и взаимодействует с многими поставщиками и потребителями, в числе которых крупнейшие мировые лидеры. Среди наших ключевых партнёров: «ЛУКОЙЛ», Красноярская железная дорога, станции, порты, поставщики лигатуры. Некоторые компании сразу готовы к диалогу и совместным проектам. Так, с портом Санкт-Петербурга, через который идёт отгрузка металла, мы работаем над повышением качества перевалки, снижением потерь, сохранностью упаковки. Другие – более закрыты для общения. Взаимодействие с ними, особенно если это крупные компании-монополисты – всегда искусная дипломатия. Прямое указание на несовершенство производственного процесса в лучшем случае не будет воспринято, в худшем – прервёт диалог компаний. К тому же перенятый без осмысления, можно сказать, навязанный опыт не принесёт эффекта.
Опытным путём мы выработали свою стратегию поведения в таких ситуациях. Главное – правильно начать диалог с руководством – акционерами и генеральным директором – и договориться о посещении их промышленной площадки. Так мы и сделали во время поездки к нашему испанскому поставщику лигатуры. Это одна из крупнейших компаний в мире и крайне важный для нас партнёр. «РУСАЛ» потребляет около 30% общего объёма их продукции, свойства которой, естественно, влияют на качество нашего готового изделия. И хотя их завод оборудован современной техникой, а процесс производства достаточно стабилен, контроль качества организован только раз в сутки. О чём мы у них аккуратно и поинтересовались, заставив задуматься, насколько грамотно производство организовано на самом деле. После важно пригласить руководство на свой завод, показать отличие выстроенной там производственной системы от традиционного подхода. Мы допускаем всех поставщиков и потребителей на наши предприятия, рассказываем об основных ценностях. Для нас это прежде всего безопасность, уважение к людям, работа в команде, эффективность и оперативность, внимание к клиентам. Как правило, после такого диалога они решают развивать у себя схожую систему.
Другой вопрос – всегда ли нужно реализовывать все принципы производственной системы или достаточно внедрить только отдельные элементы. Дискуссий по этому поводу немало. В своё время, переняв у «Тойоты» её классическую производственную систему, компании США и Европы, адаптируя её под специфику бизнеса, разделили TPS на части. Вместо оптимизации и улучшения всех процессов производства одни сосредоточились на качестве, другие – на оборудовании. Такой подход получил название lean production, а вместе с ним появился и столь популярный сегодня термин «бережливое производство».
Японцы инициативу своих последователей восприняли скептически. В принципе, понятно, почему. Без стандартизации работы невозможно решить проблему качества. Без правильной, своевременной подачи деталей не удастся организовать рабочее место. И так далее – примеров можно привести ещё много. Вывод же один: занимаясь одним вопросом, неизбежно затрагиваешь другие, и эти понятия не противоречат друг другу.
Развитие совместных с нашими партнёрами проектов по оптимизации работы, повышению качества продукции и совершенствованию логистических цепочек для «РУСАЛа» в приоритете. Но останавливаться в улучшении собственного производства, устранении «узких» мест компания тоже не планирует. Производственная система – это процесс улучшения, который не должен прекращаться никогда. Стоит остановиться, даже достигнув какого-то серьёзного уровня, и через очень короткий промежуток времени все наши успехи сойдут на нет. Главная цель TPS не какой-то результат, а развитие людей, и вот к этому мы должны стремиться постоянно.